HÄUFIGE FEHLER IN DER INTRALOGISTIK.
Ein effizienter und reibungsloser Intralogistikprozess ist entscheidend für den Erfolg eines Unternehmens.
NEWS
10 HÄUFIGE INTRALOGISTIK-FEHLER,
DIE SIE VERMEIDEN SOLLTEN.
Ein effizienter und reibungsloser Intralogistikprozess ist entscheidend für den Erfolg eines Unternehmens. Automatisierungstechnologien haben das Potenzial, die Leistung und Produktivität zu verbessern. Allerdings gibt es auch häufige Fehler, die Unternehmen bei der Intralogistik-Automatisierung begehen. Diese Fehler können zu ineffizienten Abläufen, ungenutzten Ressourcen und sogar zu finanziellen Verlusten führen.
- 1. Unzureichende Planung
- 2. Fehlende Flexibilität
- 3. Fehlende Standardisierung
- 4. Unzureichende Schulungen und Einlernphasen
- 5. Unzureichende Integration von IT-Systemen
- 6. Unterschätzung der Kosten
- 7. Fehlende Integration vorhandener Technologie
- 8. Vernachlässigung der IT-Sicherheit
- 9. Fehlende Einbindung des Menschen
- 10. Vernachlässigung der Wartung und Instandhaltung
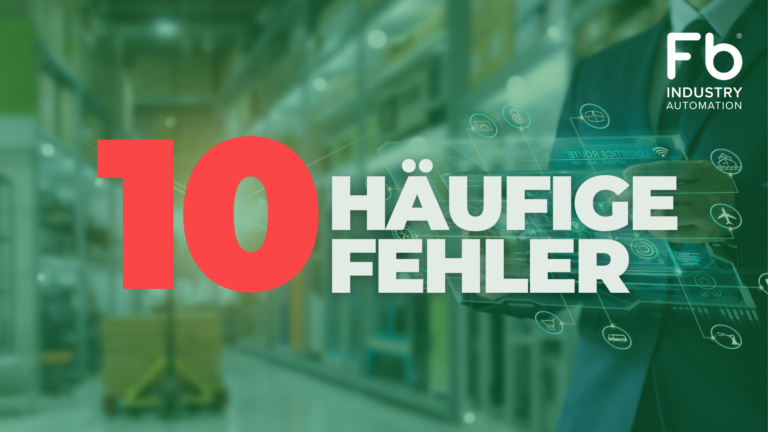
1. UNZUREICHENDE PLANUNG.
Ein häufiger Fehler besteht darin, dass Unternehmen die Automatisierung ohne ausreichende Planung und Analyse ihrer aktuellen Prozesse bzw. der spezifischen Anforderungen einführen. Es ist wichtig, eine umfassende Analyse der Abläufe durchzuführen, um die automatisierten Systeme optimal in das Gesamtsystem zu integrieren.
2. FEHLENDE FLEXIBILITÄT.
Intralogistikprozesse sind oft von Veränderungen und Anpassungen geprägt. Manchmal werden automatisierte Systeme eingeführt, die nicht ausreichend flexibel sind, um sich an sich ändernde Umstände oder Produktionsbedingungen anzupassen. Flexibilität ist entscheidend, um auf zukünftige Herausforderungen reagieren zu können. Eine zu starre Automatisierung kann zu Engpässen und ineffizienten Prozessen führen.
3. FEHLENDE STANDARDISIERUNG.
Wenn die Intralogistikprozesse nicht ausreichend standardisiert sind, kann dies die Automatisierung erschweren. Es ist wichtig, klare und einheitliche Verfahren festzulegen, bevor Automatisierungslösungen implementiert werden.
4. UNZUREICHENDE SCHULUNGEN UND EINLERNPHASEN.
Die Einführung von automatisierten Systemen erfordert ein gewisses Maß an Fachwissen und Schulung des Personals. Oft wird jedoch vernachlässigt, die Mitarbeiter entsprechend zu schulen und ihnen das erforderliche Wissen zu vermitteln, um effektiv mit den automatisierten Systemen arbeiten zu können.
5. UNZUREICHENDE INTEGRATION VON IT-SYSTEMEN.
Eine mangelhafte Integration von IT-Systemen kann zu Dateninkonsistenzen, Kommunikationsproblemen und ineffizienten Prozessen führen. Es ist wichtig, sicherzustellen, dass die automatisierten Systeme nahtlos in die vorhandene IT-Infrastruktur integriert werden.
Sie haben weitere Fragen? Dann kontaktieren Sie uns gerne. Wir helfen Ihnen jederzeit weiter.
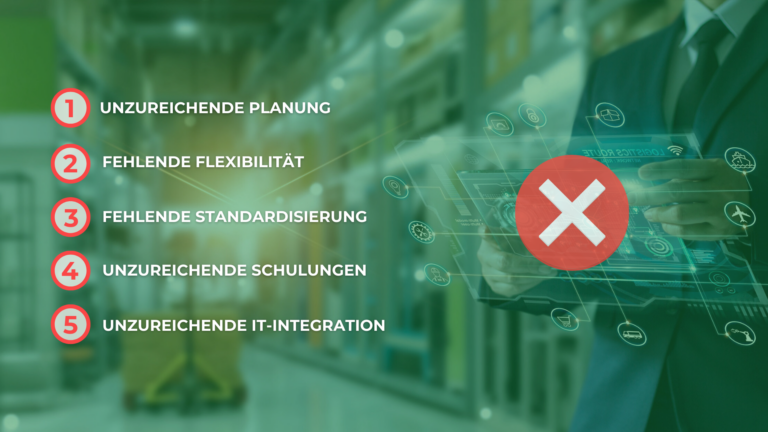
6. UNTERSCHÄTZUNG DER KOSTEN.
Automatisierung kann zunächst mit hohen Investitionskosten verbunden sein. Unternehmen müssen die langfristigen Vorteile und Kosteneinsparungen sorgfältig gegen die anfänglichen Ausgaben abwägen.
7. FEHLENDE INTEGRATION VORHANDENER TECHNOLOGIE.
Manchmal werden automatisierte Systeme eingeführt, ohne dass sie nahtlos in bestehende IT-Infrastrukturen integriert werden. Dies kann zu Kompatibilitätsproblemen und ineffizienten Arbeitsabläufen führen.
8. VERNACHLÄSSIGUNG DER IT-SICHERHEIT.
Intralogistik-Automatisierungssysteme sind oft mit dem Internet verbunden, um Daten zu übertragen und zu verarbeiten. Die Vernachlässigung der IT-Sicherheit kann zu Sicherheitslücken führen, die von böswilligen Akteuren ausgenutzt werden könnten.
9. FEHLENDE EINBINDUNG DES MENSCHEN.
Intralogistik-Automatisierung soll die Effizienz steigern, aber Menschen spielen immer noch eine wichtige Rolle in der Logistik. Es ist wichtig, ihre Fähigkeiten und Kenntnisse zu nutzen und sicherzustellen, dass sie in den Automatisierungsprozess eingebunden sind.
10. VERNACHLÄSSIGUNG DER WARTUNG UND INSTANDHALTUNG.
Automatisierte Systeme erfordern regelmäßige Wartung und Instandhaltung, um einen reibungslosen Betrieb sicherzustellen. Oft wird jedoch die Bedeutung dieser Aufgaben unterschätzt, was zu Ausfallzeiten und Betriebsstörungen führen kann.
Sie haben weitere Fragen? Dann kontaktieren Sie gerne unser Expertenteam.
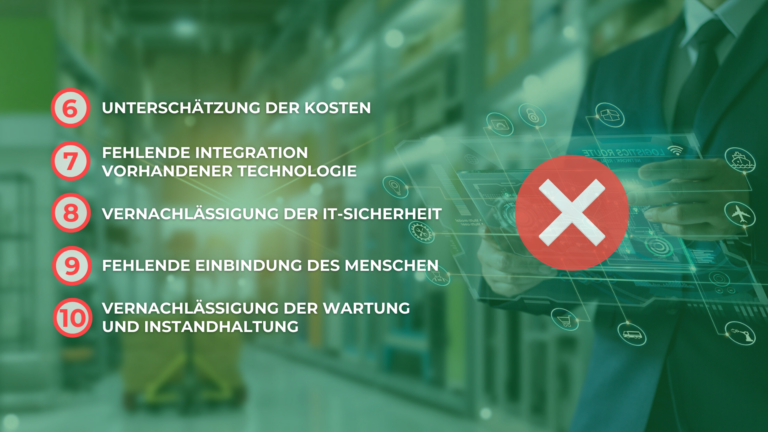
WEITERE CASES.
Automatisches Hochregallager
Die rasanten Entwicklungen im hochtechnologischen Bereich – Stichwort Industrie 4.0 – erfordern automatisierte Intralogistik Gesamtlösungen mit höchster Flexibilität und Skalierbarkeit. Das Automatische Hochregallager erfüllt diese Anforderungen und passt sich als leistungsfähiges Lagersystem individuell Ihren Rahmenbedingungen an.
Magna Steyr – Automatisches Kleinteilelager (AKL)
Erfahren Sie mehr über die Möglichkeiten eines Automatischen Kleinteilelagers (AKL) als Ersatz für ein veraltetes Regalbediengerät. Mit 19.000 Stellplätzen sorgt das Fb Kompaktlager bei Magna in Graz für höchstmögliche Kosteneffizienz. Magna ist weltweit führender markenunabhängiger Engineering- und Fertigungspartner für Automobilhersteller.
Sie sehen gerade einen Platzhalterinhalt von Facebook. Um auf den eigentlichen Inhalt zuzugreifen, klicken Sie auf die Schaltfläche unten. Bitte beachten Sie, dass dabei Daten an Drittanbieter weitergegeben werden.
Mehr Informationen